RADIOSHUTTLE™ MOVES 8700 PALLETS FOR IRELAND’S LARGEST GROCERY RETAILER
When Musgrave, Ireland’s largest privately-owned company, expanded its facilities in Kilkock, it aimed to automate the new part of the warehouse. For their “Fast Pick Area,” a Radioshuttle™ solution on a steel construction in combination with gravity rollers was chosen.
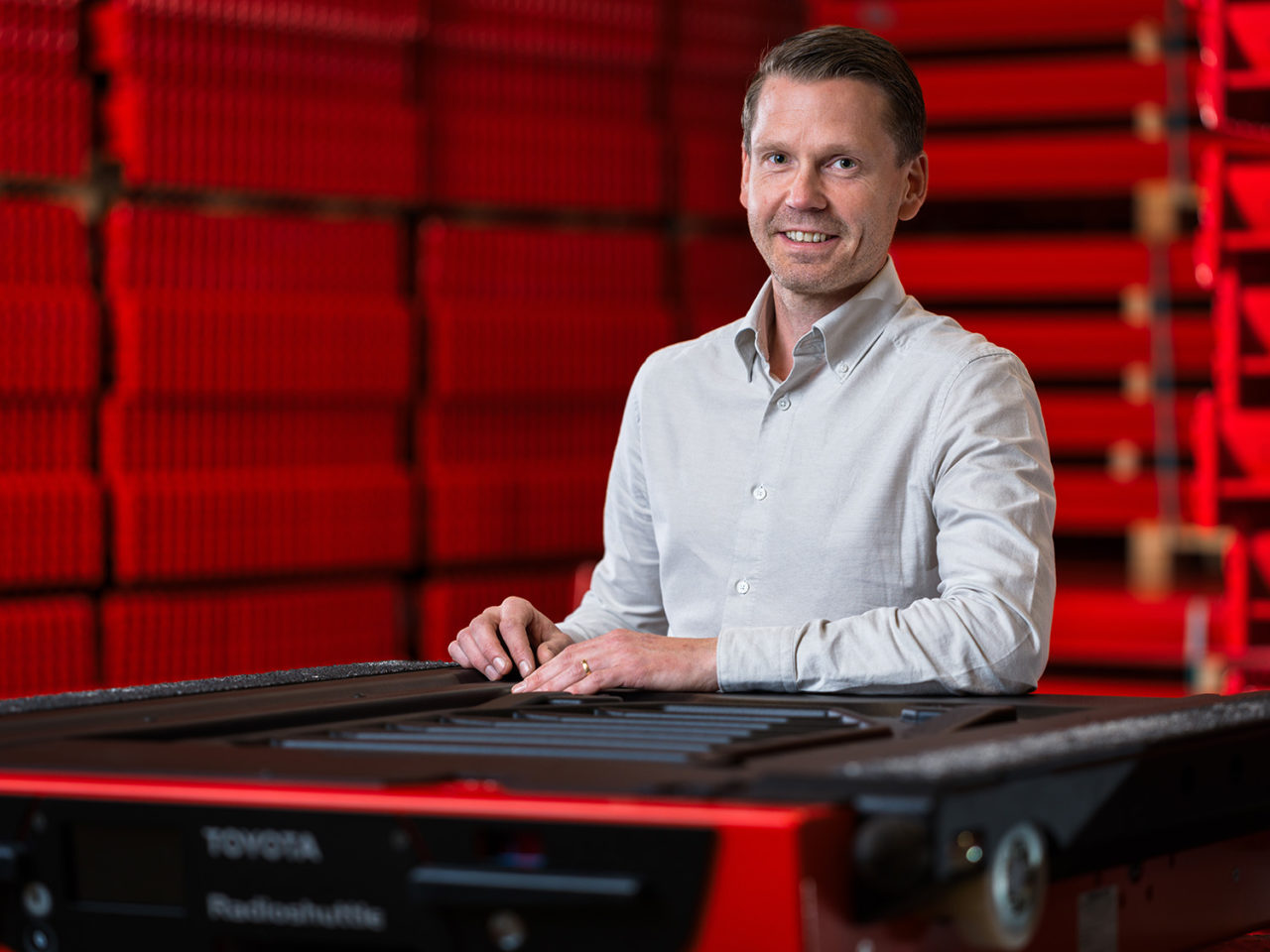
Musgrave is a sixth-generation family-owned business and Ireland’s largest grocery retailer and wholesaler, employing 40,000 people across six major warehouses.
The products in the Fast Pick Area segment are palletized by the box and handled by 12 shuttles in the Radioshuttle™ system on the steel construction. When it’s time for the products to leave the warehouse, they are picked and fed onto the gravity rollers, from where they are then picked box by box from the pallets inside the picking tunnel.
— By combining Radioshuttle with the steel construction tunnels, we could maximize the use of space. The Fast Pick area is built in four blocks, each almost 3500 m2, and the top pallet is loaded at over 13 meters in height. Typically, there would only be one picking tunnel in this type of solution, but since the installation is so large, we chose to add a crossing transit tunnel as well. This further streamlines the facility, says Magnus Saksman, Application & Design Manager at EAB Storage Equipment.
Throughout the project, there were several challenges to solve, including how to handle the empty pallets. With almost 300,000 picked items per week, there are many empty pallets to be moved away.
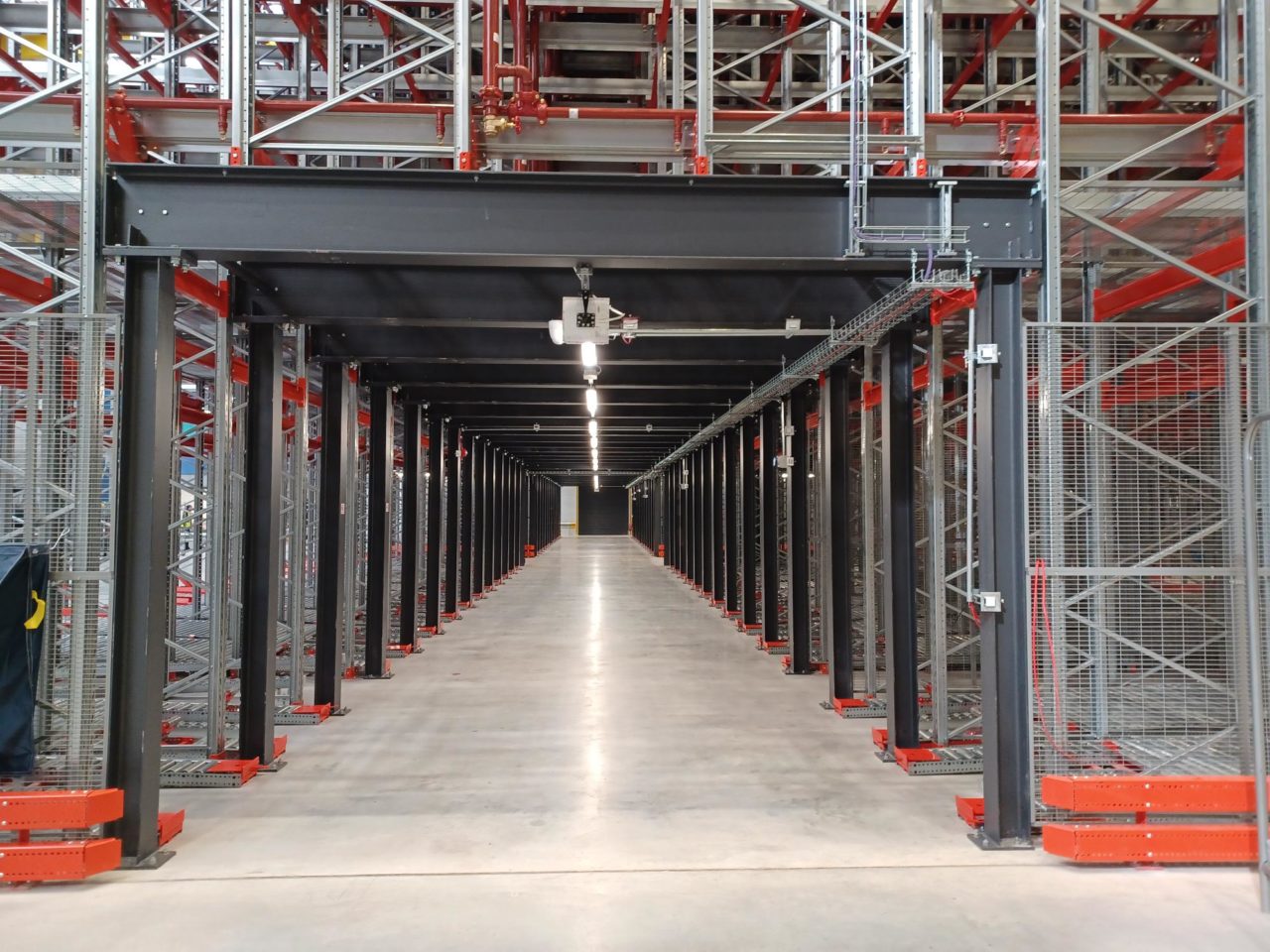
— Our suggestion to ensure the smooth handling of empty pallets was to also handle them with gravity rollers. Empty pallets often end up standing in the tunnel after picking, which is a disadvantage in several ways. There is a greater risk of truck accidents, and those picking items have less space to move. The live storage racking are always installed with a slope in the direction you want to transport the pallet, so by flipping the return gravity rollers, we handled the empty pallets outside the facility, says Magnus
The gravity rollers have been delivered with varying depths with a tiltable part to facilitate the cleaning of fallen goods. The Radioshuttle™ system has space for almost 8700 pallets, and on the rollers, 835 pallets can be loaded for picking. Each pallet weighs up to 1200 kg.
— It has truly been a fun and challenging project, with several complex solutions. The racking is high and handles many heavy pallets – we actually had to reduce the weight on the top level to get it the way we wanted. With the steel construction, we collaborated with EAB Steel Buildings, and the result simply became the pinnacle of our combined engineering. Last but not least – we met all promised delivery times and have a very satisfied customer, which is the most important thing, concludes Magnus.