Makita CHOSE EAB
Future-proofing themselves for growth by optimising their warehouse.
Makita’s Danish headquarters have been located in Horsens since 1991 and today they have more than 70 employees. Makita is a leader in power tools and accessories and this naturally requires a high level of service. Overnight delivery is one of the cornerstones, which is only possible with an extremely efficient and well-functioning warehouse.
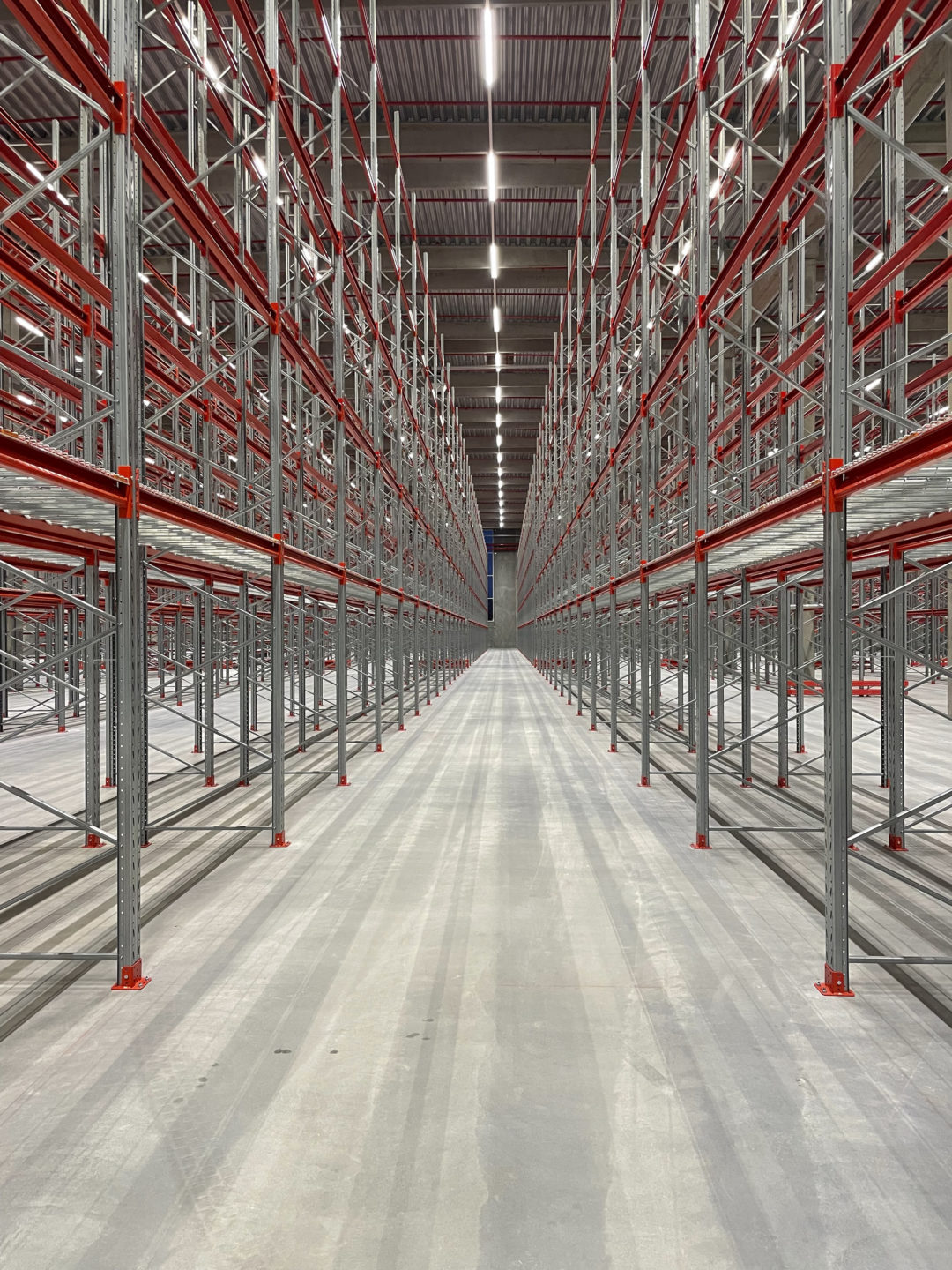
For the past 24 years, Logistics Manager Erik Boldt has kept the warehouse running as efficiently as a freshly charged Makita 18V LXT impact drill. Therefore, it was also his task to find the right supplier for the warehouse furnishings.
A good dialogue was crucial
Erik has had a good dialogue with Jes Hedelund Boelt at EAB in Denmark from before and the good co-operative relationship has continued during the almost two years that have passed from the time the new building was on the drawing board until the first pallets arrived in the impressive 17,000m2 warehouse housing 12,000 pallet spaces. For Erik, it wasn’t just a question of price and getting the solution that could accommodate as many goods as possible. He emphasised the importance of having a good personal relationship with the supplier, which was ultimately decisive in Makita’s choice of EAB as a partner.
Anti-collapse design shows strength in the event of a collision
Shortly after the final installation was done, the safety of the pallet racking was tested in live mode. One of the warehouse’s experienced lorry drivers drove into one of the rows of pallet racks at high speed. This type of accident could have had major consequences had it not been limited by the energy-absorbing design of the scaffolding. The fact that even the smallest parts, such as nuts and bolts, are well dimensioned in EAB’s racking, minimises the damage when an accident occurs. The pallets that were not directly affected by the collision remained undamaged and the damage was repaired by EAB within a week.
In addition to creating greater security and facilitating internal work, the investment has also improved customer service, allowing Makita to stay ahead of its competitors in terms of service and delivery. Overall, optimising its inventory has been a big win for Makita.
EAB has been involved throughout the process, supplying pallet racks, nets and collision protection. In addition, EAB has of course also been responsible for the installation and managed subsequent service inspections.